Benefits, challenges when sheet metal meets the tube business
Some precision sheet metal operations are pursuing a one-stop-shop strategy that includes tube fabrication. Any new venture involves risks, but with the right approach to tube, a fabricator can reap the rewards.
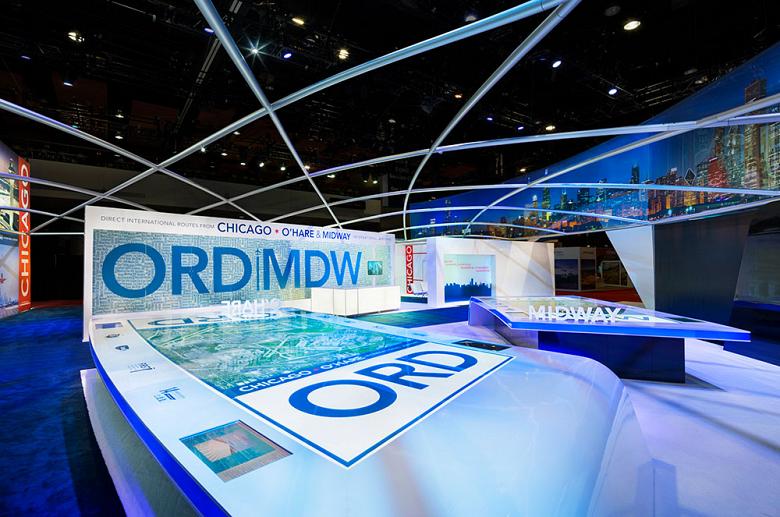
The Metal Shop fabricated the tubular structure that spans this tradeshow exhibit. The tube replicates the structure over the bandshell in Chicago’s Millennium Park. Photo courtesy of The Metal Shop.
It’s easy for a custom fabricator to consider tube cutting and bending as an extension of sheet metal work, especially as more companies bill themselves as one-stop shops. Need a formed sheet metal assembly with tubular components? Perhaps a tube cut on a laser—be it fixtured on a flat-bed system, on a rotary axis, or sent through a dedicated laser tube cutting machine? A tube cut with tabs and slots that mate perfectly to a formed and assembled enclosure? Or perhaps tube takes weight out of a product, be it for some type of vehicle or modern construction built on hollow structural section tubes.
Flat sheet and round or shaped tube seem to be part of the same continuum of work. Tube is sheet metal, after all, just shaped, right?
Not really, as any custom fabricator who has tackled tube fabrication—specifically, tube cutting and bending—will tell you. Specialty tube fabricators exist for a reason. The work requires significant investment in people and technology. And compared to sheet metal, tube is in many respects a different animal.
Delving into any new technology has risks. The business may not be sustainable. It’s difficult to find people who really know tube. Customers may not think differently and accept suggestions for making cost-effective tubular designs. But a fabricator with the right approach can mitigate these risks and, ultimately, reap the benefits.
A One-Trick (or One-Tube) Pony
Don Kammerzell, president of K-zell Metals, a custom fabricator in Phoenix, recalled visiting fabricators with plenty of flat sheet laser cutting, precision bending, the works, along with a lone, idle tube bending machine in the corner. When he asked about the machine, he usually heard the same response: A major customer asked if the shop could perform a few significant tube bending jobs, and the fabricator obliged. Technicians set up the machine and tools to run one identical part after another. Pretty soon it seemed like the shop had tapped another revenue stream, and all seemed right with the world.
“Those parts justified the machine investment,” Kammerzell said. “[These shops] have operators, but they don’t really have setup people, because they don’t change out jobs very often.”
Then the contract ended, and the shop was in a bind. It had no tube bending tooling to speak of besides the tools for the job it already ran, and it employed an operator who knew how to set up only a few parts.
If the shop sold more tube bending work, it soon found that the inadequately trained, inexperienced operator would take forever to set up a new job. Tools are expensive, so the shop also found it difficult to compete with neighboring operations with large tube bending tool libraries. Not too long after, the shop abandoned the tube bender, leaving it to gather dust in a corner.
Kammerzell kept these thoughts at the back of his mind when an opportunity arose. “We got into tube bending when we couldn’t find anyone who was doing job shop tube bending work near us,” he recalled. “Customers kept approaching us. Eventually, though, opportunity struck. We stumbled on a used machine, with a lot of tooling.”
Kammerzell emphasized the last part—the tooling. The used machine itself looked like a steal, but Kammerzell said he wouldn’t have looked at it seriously if it weren’t for the tooling, all 60 sets of it. Maintaining that tooling is critical, and the tooling Kammerzell bought had been well taken care of. “Just the other day, we had a job that called for a tool in our tooling library. The tool was from 1954.”
Tools will last if taken care of, though most qualify that statement, because tool life depends on the application, the tube bending machine, and—perhaps most significant—how the operator treats them.
Specifically, the operator must use the right tools for the job, and not just “make it work” for a specific tool set. A tool set may fit loosely to the tube for various reasons. The tool may not be suited for the job or maintained well. Or the tube geometry itself is inconsistent—a big reason some shops standardize tube purchasing practices, matching certain tube vendors with certain jobs, to ensure tube setups are as consistent and repeatable as possible.
“Are your tools tight to the tube, or are they loose? That space can cause the tube to mark, wrinkle, or even collapse,” said Scott Mitchell, president of OMNI-X, an Englewood, Colo.-based tooling provider, speaking of tool wear factors in rotary draw bending. When fabricators enter the tube market, they should ensure operators have the right tools for the jobs at hand, “and not just use tools for a similar sized application, expecting they’ll work.”
He added that a little more tooling investment upfront can help a shop overcome the chicken-and-egg scenario when it comes to building a tooling library. He didn’t suggest fabricators just buy a vast array of tools from the get-go, but he did suggest ways fabricators can make certain tooling components apply to multiple jobs.
An example would be pressure dies in rotary draw bending. “Your initial application may need to bend 180 degrees over a short radius, so usually you would have a pressure die to support that short radius. But then you get a job for the same tube, only bent over a larger radius. If you purchase a longer pressure die from the start, that one tooling component could be used for multiple jobs.” He added a shop can also gain some flexibility by using inserted bend dies with interchangeable grip sections, which accommodate different grip lengths.
One can get deep into the weeds when it comes to bend tooling, and the same applies to tube cutting, particularly laser tube cutting. This brings up another risk (and potential reward) of tube fabrication: finding talent.
Who Owns the Process?
Todd Swift and Michael Cousins go back about as far as you can go. “He’s my friend’s son, and I was at the hospital the day he was born,” said Swift, who today is vice president of operations at The Metal Shop, a small custom fabricator in Pleasant Prairie, Wis. Little did Swift know that the baby he met in the hospital decades ago would become the cutting and bending guru who has made The Metal Shop’s venture into tube fabrication a resounding success.
The sheet metal fabricator got its start serving firms that design tradeshow booths, and tradeshow exhibits still make up the majority of its business. The company’s fabrications have been seen at major tradeshows and other events, even the World Economic Forum in Davos, Switzerland. The high-profile ICEhouse™ structure in Davos was a showcase for sustainable building, and it served as the media center at the World Economic Forum. Presidents, royalty, and celebrities have stood within The Metal Shop’s handiwork.
For those fabricating for the exhibit sector, turning around work in a week is no big deal, and a two-week lead time seems like forever. It requires hard work and engaged talent—like Cousins. “We once had a longtime tube laser technician come and watch our operation,” Swift recalled. “After watching [Cousins], he told us, ‘He’s the smartest kid I’ve ever seen running a tube laser machine, period.’”
Interestingly, Cousins never received formal training; he simply has a curious mind and a knack for shop work, from welding to programming the press brakes, to running the laser tube cutting system, even the rotary draw tube bender.
Swift recalled one job for an exhibitor who wanted thin-walled tube bent to an angle so tight that under normal circumstances, the tube would wrinkle and collapse. But then the team had an idea.
The tube’s cosmetics didn’t matter, since it would be hidden behind a display. What if Cousins placed relief cuts on one side of the tube using the laser? The tube then could be formed with a portable manual bender, wheeled right where cut tubes emerged from the laser. The relief cuts allowed the tube to be bent to a tight angle without wrinkling.
The creativity doesn’t stop there, especially when time is of the essence. For several extremely quick-turn jobs, the company has cut tubes in the tube laser in such a way so that, in the final assembly, they aren’t tubes at all but instead a radiused edge of a larger sheet metal structure. “This way you don’t have to use the press brake,” Swift said.
This shows how the possibilities abound if a shop employs someone with a curious mind who learns and eventually owns the ins and outs of tube fabrication. “You’re really just hampered by your imagination,” Swift said.
Modern software helps, making the learning curve less severe than it was, and Phil Kooima remembers that steep learning curve well. Kooima is president of Rock Valley, Iowa-based Kooima Co., a large and diverse custom fabricator that does extensive laser tube cutting and bending, complementing the shop’s flat sheet cutting and bending capabilities. An early adopter of technology, the company purchased its first tube laser 18 years ago.
“The software didn’t exist [for our machines] back then,” Kooima said. “So we had to program the G and M codes at the machine manually, line by line.”
Software has come a long way since then, both for programming and inspection. At K-zell, for instance, the tube bending operator uses an inspection arm with a special attachment that measures the tube immediately after it emerges from the company’s hybrid electric-hydraulic tube bending machine (which has replaced the used tube bending machine that launched K-zell into the tube bending arena). The inspection system compares the tube OD, radius, straight lengths, and bend angles with the original 3-D CAD model, then feeds the necessary corrections back to the CNC tube bender.
Still, despite software advances, Kammerzell emphasized that the shop’s tube operation wouldn’t be where it is without talent, especially in tube bending. If a tube isn’t bent right the first time, there’s no hitting the part again, like with an underbent part on a press brake. The tube is scrapped, and the setup person makes the adjustments and tries again.
“The machine is absolutely unforgiving. You need to document your setup adjustments to the nth degree. For instance, our machine has a hydraulically actuated over-the-center clamping die. When you get it in place, you tighten a lead screw. You need to know and document the exact position of that lead screw. And you need to make and document more than a dozen similar measurements like that.
“If you make a mistake, you will pay for it. We’re so lucky to have talented people who can perform multiple setups and bend small quantities,” Kammerzell said.
Employing such knowledgeable and curious people, a fabricator’s creativity with tube can thrive and help the business grow—if, that is, the fab shop finds and works with the right customers.
Not Just a Part Number
At Kooima Co., being able to collaborate with customers is the very reason the organization performs such a wide variety of fabrication processes, including tube cutting and bending.
“If we’re bidding on a job and we’re just a part number on a customer’s Excel sheet, we just can’t win,” he said, adding that Kooima doesn’t employ salespeople who sell tube fabrication exclusively. They treat tube fabrication as a family of manufacturing steps that can add value to a broader project.
Kooima expects tube will continue to play a larger role in more markets, especially considering trends in buildings, farm, construction equipment, and recreational vehicles like ATVs. Tubes are showing up everywhere.
“Many tubular parts we produce would have been sheet metal stampings just 15 years ago,” he said. “We’re only halfway through the tube revolution, I think. There’s a lot of runway in this business, and I’m very optimistic.”
Source: thefabricator